The use of v-belts is essential in driving efficiency and reliability in various mechanical systems. These belts, characterized by their trapezoidal cross-sectional profile, play a crucial role in power transmission applications, delivering robust performance across diverse industrial settings. Their unique design is tailored to enhance the grip and contact surface area, minimizing slippage and ensuring seamless torque transfer between connected components.
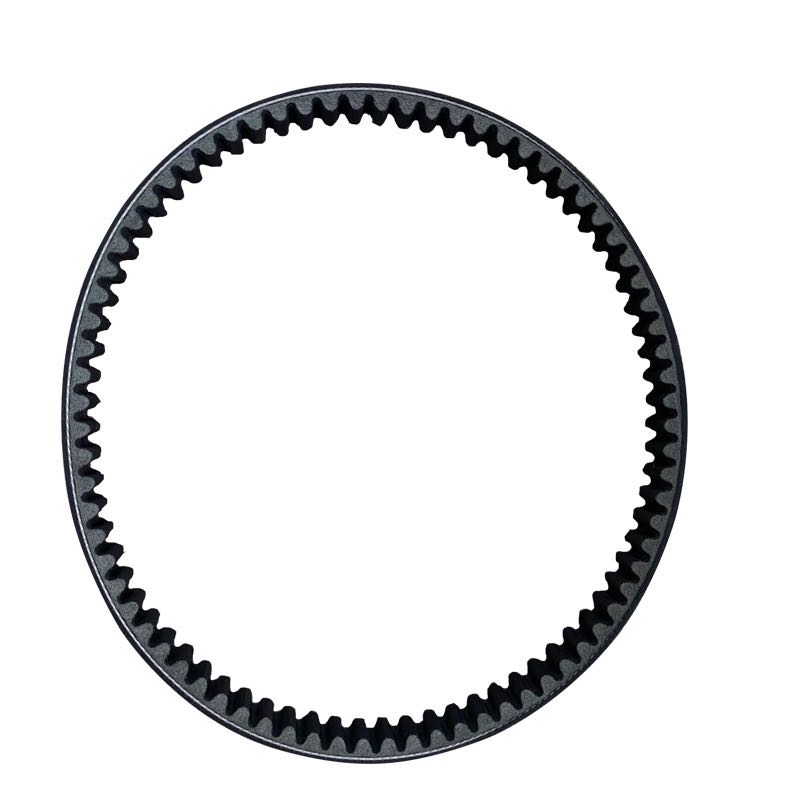
Crafted from materials such as rubber, neoprene, or polyurethane, v-belts are reinforced with tension-bearing fibers like polyester or Kevlar. This construction offers exceptional strength and durability, making them suitable for high-tension applications. The composition of a v-belt directly influences its operational longevity and effectiveness, thereby making the choice of materials a critical consideration for engineers and technicians.
In industries such as manufacturing, automotive, and agriculture, v-belts are indispensable. They connect driving pulleys to driven pulleys, facilitating the movement of various machinery parts with precision and reliability. In automotive engines, for instance, v-belts are integral in operating alternators, water pumps, and air conditioning compressors, highlighting their significance in maintaining vehicular functions and performance.
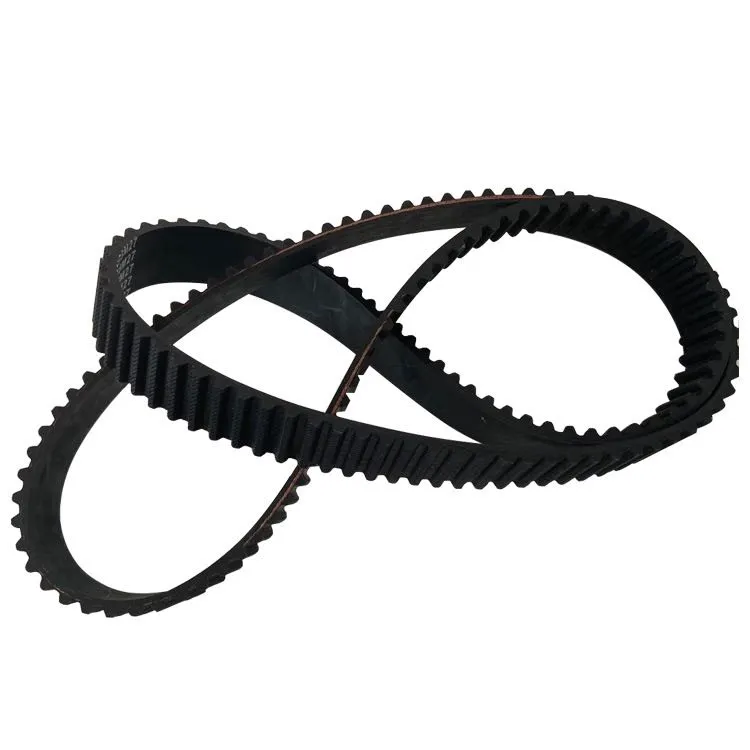
The expertise required to select the right v-belt involves understanding several crucial factors, including belt tension, pulley alignment, and the environmental conditions of operation.
Proper installation and maintenance are also paramount in optimizing the belt's efficiency. When belts are too tight, they can lead to increased bearing load and reduced bearing life, whereas overly loose belts may slip, causing elevated wear and decreased efficiency. Thus, achieving optimal tension is vital in extending the lifespan of both the belt and the machinery it powers.
v-belts
Authoritative insights into v-belt technology emphasize continuous innovation aimed at improving energy efficiency and reducing wear. Modern advancements have introduced new belt profiles, such as cogged or ribbed variations, designed to reduce bending stress and frictional heat, thereby enhancing overall performance. These developments reflect the industry's commitment to delivering high-performance solutions that meet evolving industrial demands.
Experts in the field consistently advocate for implementing regular maintenance schedules to inspect and replace worn belts. Such initiatives prevent catastrophic machine failures that can result in operational downtime and substantial financial losses. The incorporation of routine inspections ensures that any signs of wear, such as cracks or glazing, are addressed promptly, safeguarding the operational integrity of the machinery.
Trustworthiness in v-belt manufacturers is enhanced by adhering to rigorous quality standards and offering warranties that guarantee performance. Selecting a reputable brand ensures that the belts comply with industry regulations and customer expectations for safety and reliability. Additionally, comprehensive product documentation and customer support provide end-users with valuable resources for troubleshooting and resolving any operational issues that may arise.
In conclusion, v-belts represent a foundational element in power transmission systems, their meticulous design and construction reflecting the high standards expected in industrial operations. By selecting the appropriate belt type, ensuring proper maintenance, and choosing a trusted manufacturer, industries can achieve sustained operational efficiency and reliability. The continuous advancement in v-belt technology underscores a commitment to meeting the growing demands of power transmission applications, making them indispensable in today's mechanically driven world.