V-belt pulleys, often considered the quintessential component in power transmission systems, play a critical role across various industries. Their design and functionality are paramount in ensuring efficiency, reliability, and longevity of machinery. This article aims to delve deep into the nuances of V-belt pulleys, enhancing understanding from both a technical and practical perspective to help businesses make informed decisions.
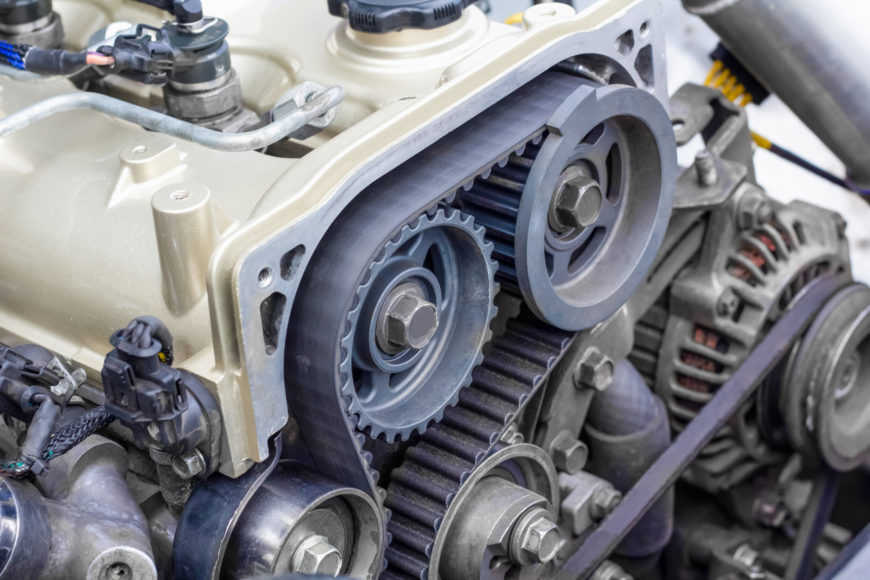
In the world of mechanical engineering, V-belt pulleys are revered for their ability to transmit power between axles using a loop of belt. The name V-belt originates from the belt's cross-section that is shaped like a V. This geometric feature allows for increased friction and better grip, crucial for transferring power effectively. When selecting a V-belt pulley system, it's not merely about the wheel; the entire ecosystem including material composition, groove design, diameter, and alignment play vital roles.
First and foremost,
material selection in V-belt pulleys is crucial. Cast iron, steel, and aluminum are the most common materials used. Each offers distinct advantages. For instance, cast iron provides robustness and vibration damping, ideal for heavy-duty applications. Steel is known for its strength and resistance to wear, making it suitable for high-speed applications. Aluminum, on the other hand, offers lightweight advantages which can be beneficial in high-speed, low-load scenarios.
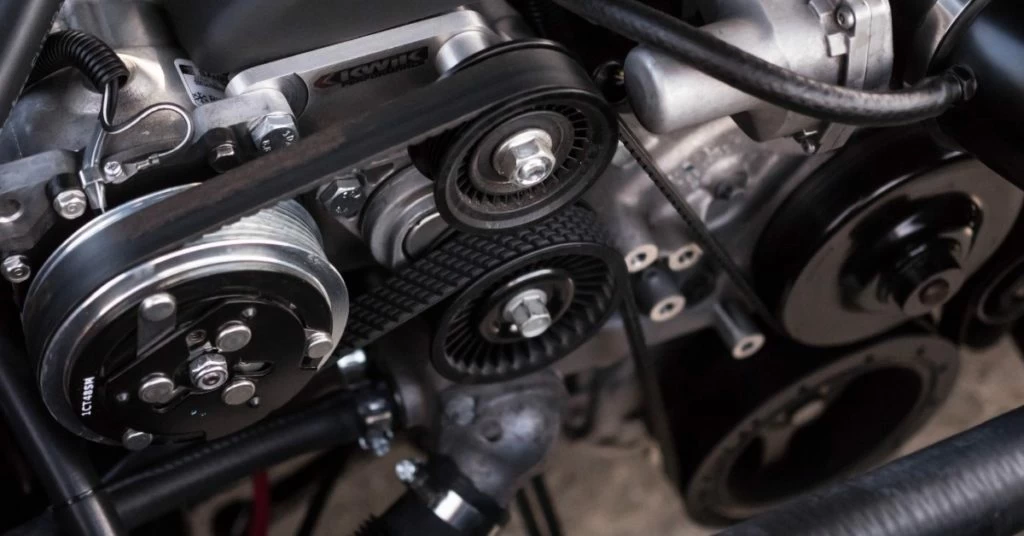
One cannot overstate the importance of precise groove design in V-belt pulleys. The groove design must perfectly match the belt profile to maximize friction and prevent slippage. A misalignment or mismatch can lead to rapid wear and system inefficiency. In this vein, the angle of the groove is pivotal. A standard groove angle is about 40 degrees, but customization might be required based on the application specifics. Companies investing in the right groove design often find a significant reduction in downtime and maintenance costs.
v belt pulley
The diameter of the pulley also significantly impacts performance. Larger diameters are preferable for reducing belt wear and enhancing belt life, as they allow for smoother operation. However, they also mean slower speed and larger size, which may not be suitable for compact machinery. Conversely, smaller pulleys can lead to faster speeds but may cause increased belt wear and require more frequent replacements. Thus, striking the right balance is necessary for optimal performance.
Alignment is another crucial aspect often overlooked. Misaligned pulleys can lead to lateral forces on belts, causing premature wear and even system failure. Utilization of laser alignment tools has emerged as a game-changer in ensuring precise alignment, thereby extending the life of both the belt and pulley and maintaining system integrity. Consistent monitoring and maintenance of alignment can save significant resources in the long run.
In terms of maintenance and upkeep, V-belt pulleys are generally low-maintenance compared to other power transmission methods. However, regular inspections are advised to ensure they remain in optimal condition. Checking for signs of wear, such as polished sidewalls on the belts or unusual noises, can preempt major system failures. It's advisable for operators to keep a regular maintenance schedule and engage with reputed suppliers for quality spares.
In conclusion, V-belt pulleys, though often underestimated, are a cornerstone of efficient mechanical operations. Understanding the intricacies involved in their selection and maintenance can significantly impact an enterprise’s productivity and cost-efficiency. As technology progresses, innovations in materials and design are poised to enhance their performance further. Leveraging expertise from seasoned professionals can aid in tailoring solutions that meet specific industry requirements, enhancing system reliability and longevity. By prioritizing quality and precision in V-belt pulley systems, businesses can ensure that their machinery not only meets current operational demands but is also equipped for future challenges.