Ribbed drive belts, a vital component across many industries, are engineered to offer optimized power transmission in a myriad of mechanical systems. Their unique design, incorporating longitudinal ribs, enhances flexibility and tracking, making them indispensable in modern machinery, from automotive engines to complex industrial applications.
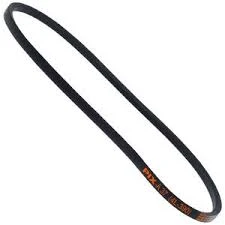
A distinctive feature of ribbed drive belts is their extraordinary capability to manage high load applications without compromising operational efficiency. These belts boast a multi-rib structure, akin to a blend of flat and V-belts, facilitating an impressive balance between grip and flexibility. This design ensures that the belts can transfer power seamlessly even in compact configurations, a scenario often encountered in automotive engines where space and weight are at a premium.
The construction materials of ribbed drive belts significantly contribute to their superior performance and longevity. Typically, high-tensile synthetic cords are embedded within the belt, coupled with specially formulated rubber compounds. This blend not only imparts robustness and resistance to wear but also mitigates issues commonly associated with temperature fluctuations and oil contamination, thus expanding their operational lifespan.
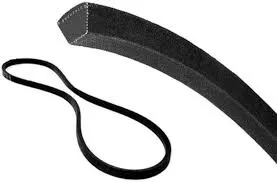
In terms of expertise, choosing the appropriate ribbed drive belt involves assessing several critical parameters. The application type, load requirements, and environmental conditions should be taken into account. For example, automotive applications demand belts that can withstand high-speed operations and frequent stop-start conditions, where the ability to resist thermal degradation is paramount. On the other hand, industrial applications may prioritize belts that can handle uneven loads or operate in harsh environments.
Authoritativeness in ribbed drive belt technology is primarily evidenced through adherence to rigorous industry standards and testing protocols. Manufacturers typically engage in extensive testing regimes, ensuring products meet or exceed OEM specifications. This dedication to quality control measures builds trust and positions them as leaders in the sector. Furthermore, many leading brands offer comprehensive customer support and detailed technical documentation, assisting users in making informed decisions about installation, maintenance, and troubleshooting.
ribbed drive belts
Ensuring trust when selecting a ribbed drive belt provider is crucial. Auditing the track record of prospective suppliers, including their history of innovations and customer testimonials, can provide valuable insights. Brands with a reputation for delivering reliable, high-performance products, backed by warranties and solid aftersales support, often emerge as the preferred choice for industry professionals.
The choice and maintenance of ribbed drive belts are equally critical in optimizing their performance and extending their service life. Regular inspections to identify signs of wear, alignment, and tension checks are essential maintenance practices. Employing predictive maintenance strategies can also preemptively identify potential issues such as misalignment or tension deviations, thereby preventing unexpected downtimes.
To gain experiential insights, it’s beneficial to engage with communities and forums where industry veterans discuss practical experiences and share solutions to common challenges associated with ribbed drive belts. These platforms can be valuable resources, offering firsthand advice on achieving optimal operational performance and troubleshooting complex issues.
In conclusion, ribbed drive belts are indispensable for modern mechanical systems, given their superior ability to transmit power effectively in diverse applications. Experts recommend selecting belts tailored to specific operational requirements and maintaining them diligently to harness their full potential. By understanding the technical specifications and leveraging proven expertise, businesses can make informed decisions that enhance operational efficiency and equipment longevity.