Toothed belts, commonly referred to as timing belts or synchronous belts, play a pivotal role in a diverse range of machinery and automotive applications. Understanding the various types of toothed belts is crucial for anyone looking to optimize machinery performance, enhance durability, or improve efficiency. This article delves into the different types of toothed belts available, highlighting their unique features, applications, and benefits, with insights drawn from industry expertise and real-world experience.
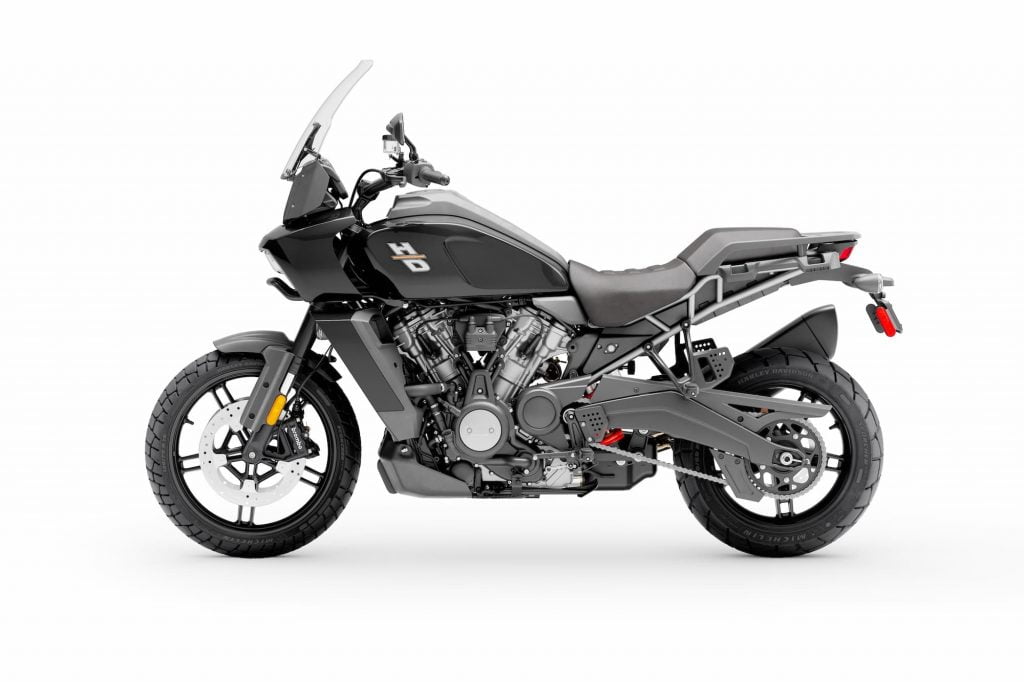
Firstly,
one of the most common types of toothed belts is the trapezoidal timing belt. Characterized by their trapezoidal tooth profile, these belts are often found in traditional car engines and simple machinery. They excel in applications requiring moderate precision and load-carrying capacity. Their design ensures reliable power transmission and positioning, making them ideal for basic automotive timing needs and some industrial applications. However, their effectiveness can be limited by factors such as high levels of wear and lower resistance to dynamic loads compared to curved tooth profiles.
Moving onto a more advanced variant, the rounded or curvilinear timing belts have gained popularity due to their superior load distribution capabilities. These belts feature teeth with a rounded profile, allowing for smoother engagement with the pulleys and significantly reducing tooth stress. This design is pivotal for high-performance automotive engines and complex machinery where precision and reduced vibration are crucial. The GT2 and HTD (High Torque Drive) belts are typical examples, offering improved performance for 3D printers and CNC machines, where precision and efficiency are essential.
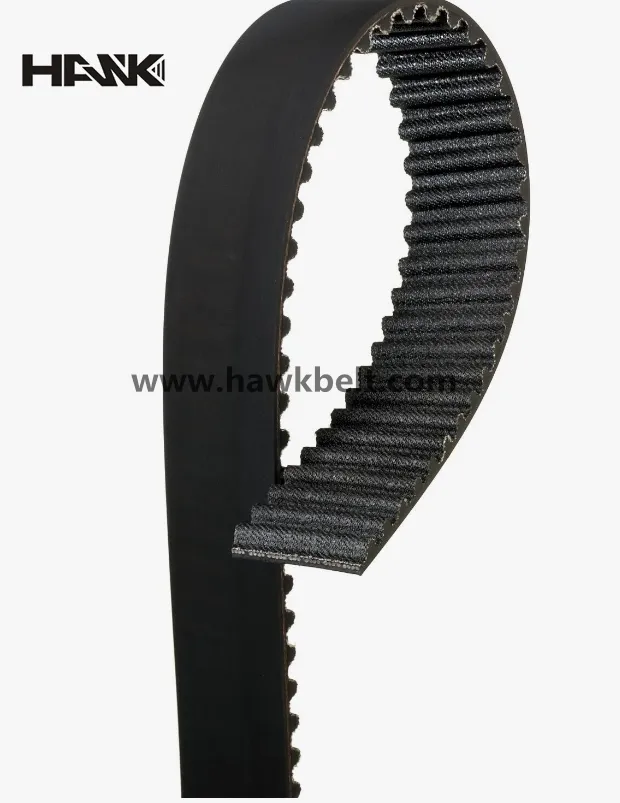
The third category, synchronous belts with modified tooth profiles, includes advanced designs like the RPP (Reinforced Parabolic Profile) and the Poly Chain GT Carbon belts. These belts are engineered for high torque and power applications, combining a unique tooth shape and construction material for optimal performance. Utilizing materials like carbon fiber-reinforced polyurethane, these belts are incredibly durable and effective in industrial settings where heavy-duty performance is non-negotiable. They are renowned for their longevity and ability to maintain performance under harsh conditions, making them a preferred choice for large mechanical systems and heavy machinery.
Specialty toothed belts, such as those designed for wet or oily environments, are also crucial in specific industrial applications. These belts often feature resistant coatings or materials to withstand chemical exposure, moisture, and extreme temperatures. Examples include waterproof belts used in food processing and medical equipment where hygiene and belt lifespan are paramount. The development of these specialized belts stems from a need for a reliable power transmission solution in environments that pose a risk to conventional belt materials, reflecting the industry's ongoing innovation tailored to niche applications.
toothed belt types
Selecting the appropriate toothed belt type demands consideration of several factors, including the application's operational environment, load requirements, and desired lifespan. Utilizing a belt unsuitable for its intended use can lead to reduced efficiency, increased wear, and potential machine failure, highlighting the importance of selecting the right belt type.
In terms of maintenance, toothed belts generally require less attention compared to chain drives or gear systems, offering an advantage in reducing downtime and maintenance costs. However, regular inspections for signs of wear, misalignment, or improper tensioning are necessary to preserve their optimal performance and prevent costly breakdowns.
Utilizing experience from field applications, one can appreciate that while each type of toothed belt has specific advantages, the choice must align with the specific operational demands and technical requirements. Thus, an understanding not just of the mechanical properties, but also of the environmental conditions and user expectations, is crucial in making an informed decision. Enlisting expert advice and leveraging authoritative resources are strategies for ensuring the choice aligns with best performance practices, sustaining machinery efficiency and longevity.
In conclusion, the various types of toothed belts offer solutions to a wide array of mechanical challenges, each with its unique set of advantages. From basic timing requirements to high-performance demands, understanding these distinctions and choosing well ensures peak operational efficiency and equipment reliability.