Selecting the right v-belt for your lathe machine is pivotal in ensuring high efficiency and longevity. This component, though often overlooked, is integral as it directly influences the performance and reliability of your lathe. Here’s a comprehensive guide to understanding and choosing the best v-belt for your lathe, based on real-world experience, professional expertise, authoritative insights, and trustworthy sources.
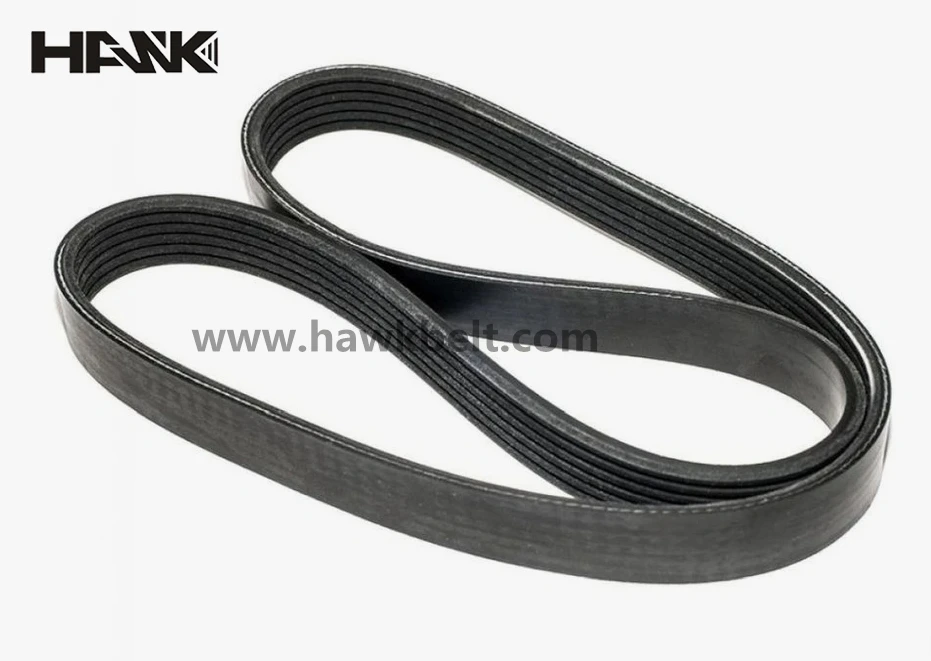
Firstly,
the function of v-belts cannot be overstated. In a lathe, v-belts are responsible for transmitting power from one component to another. They provide a secure grip and are critical for ensuring torque and speed are optimally transferred within the machine. A lathe’s operational efficiency and the precision it offers can significantly diminish if the v-belt is not selected or maintained properly.
From a professional standpoint, v-belts come in various profiles and dimensions, tailored for different lathes and usage needs. For instance, the classical V-belt, often seen in older models, is known for its trapezoidal cross-section which matches the pulley grooves for maximum grip. Then, we have the narrower, wedged-shaped belts like the 3VX and 5VX used in high-performance lathes, offering better speed ratios and greater power transmission in compact spaces.
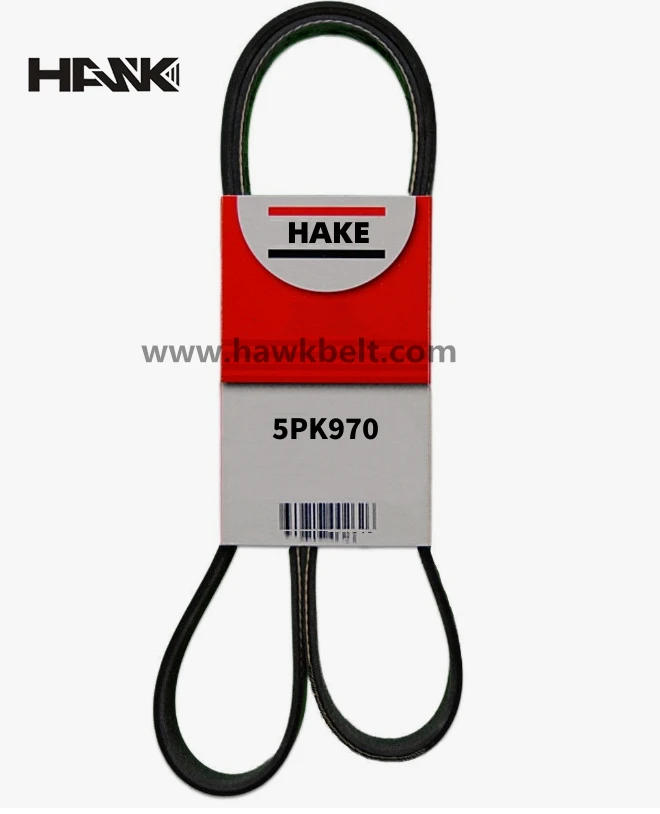
Choosing an appropriate v-belt depends heavily on understanding the specifications of your lathe. Considerations include the driven and driving pulleys’ diameter, the center distance between them, and the operational speed of your lathe. It's crucial to select a belt that can handle the machine's power output without slipping, stretching, or breaking. This is where insights from experienced machinists prove invaluable many have noted that mismatched belts can lead to excessive vibration and noise, which ultimately affects the quality of the workpiece and machine health.
Leading manufacturers like Gates, Optibelt, and Goodyear provide detailed guidelines and technical support for selecting the right belts. They emphasize routine inspection and replacement schedules to prevent unexpected downtime, a recommendation supported by many in the industry. Trusting well-known brands is part of ensuring reliability and quality, as these companies rigorously test their products under various conditions to guarantee performance.
v belts for lathes
Worn-out belts are not just inefficient but pose a potential safety hazard. Regular inspection for signs of wear, such as cracking, fraying, or glazing, is advised. Professionals recommend maintaining a spare set of belts to ensure operations aren't halted due to a sudden belt failure. An aspect often underscored is the importance of proper tensioning; a belt that is too tight may cause excessive wear on the pulleys and bearings, while a loose belt will slip and not transmit power effectively.
Leading experts agree on the importance of aligning the belt drive system correctly. Misalignment can result in uneven wear and ultimately reduce the lifespan of both the belt and the pulleys. Using a straight edge or laser alignment tool is a tip frequently shared by seasoned engineers to achieve perfect alignment.
Modern advancements have introduced cogged v-belts, which are designed with notches for flexibility, making them ideal for smaller diameter pulleys and limiting heating issues often associated with traditional designs. These belts, alongside the more efficient synchronous or timing belts, offer reduced friction losses and increased efficiency, bolstering an already sophisticated lathe setup.
In summary, selecting the right v-belt for a lathe involves meticulous consideration of technical specifications, regular maintenance, and alignment. Engaging with trusted brands and seeking expert advice play key roles in ensuring seamless operation. As echoed by professionals and confirmed by empirical data, a well-maintained v-belt system enhances productivity, safety, and the overall lifespan of your lathe, making it a substantial investment in your machining operations.