Selecting the right fan belt size is essential for the proper functioning and longevity of machinery, whether in automotive systems, industrial applications, or agricultural equipment. Identifying the correct size ensures smooth operations, energy efficiency, and prevents untimely wear. Herein lies the importance of understanding the complexities of fan belt sizing through real-world experiences and expert insights.
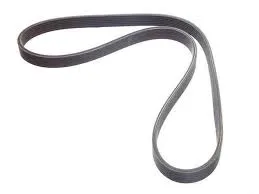
A fan belt, often referred to as a drive belt or serpentine belt, is crucial for transferring rotational power from one component to another in a system. While deceptively simple at first glance, these components are precisely engineered to meet the specific needs of various machines. A fan belt that's too tight can cause excess tension on bearings and pulleys, while a loose one may slip off, leading to overheating or mechanical failure.
The first step in ensuring you have the right fan belt size involves comprehensively understanding the machinery's specifications. Manufacturers typically provide clear guidelines on the optimal belt dimension, including parameters like length, width, and thickness. These metrics determine how effectively a belt can manage load and transfer energy. Different systems may have unique requirements; thus, consulting the equipment’s manual or manufacturer's website is a paramount step.
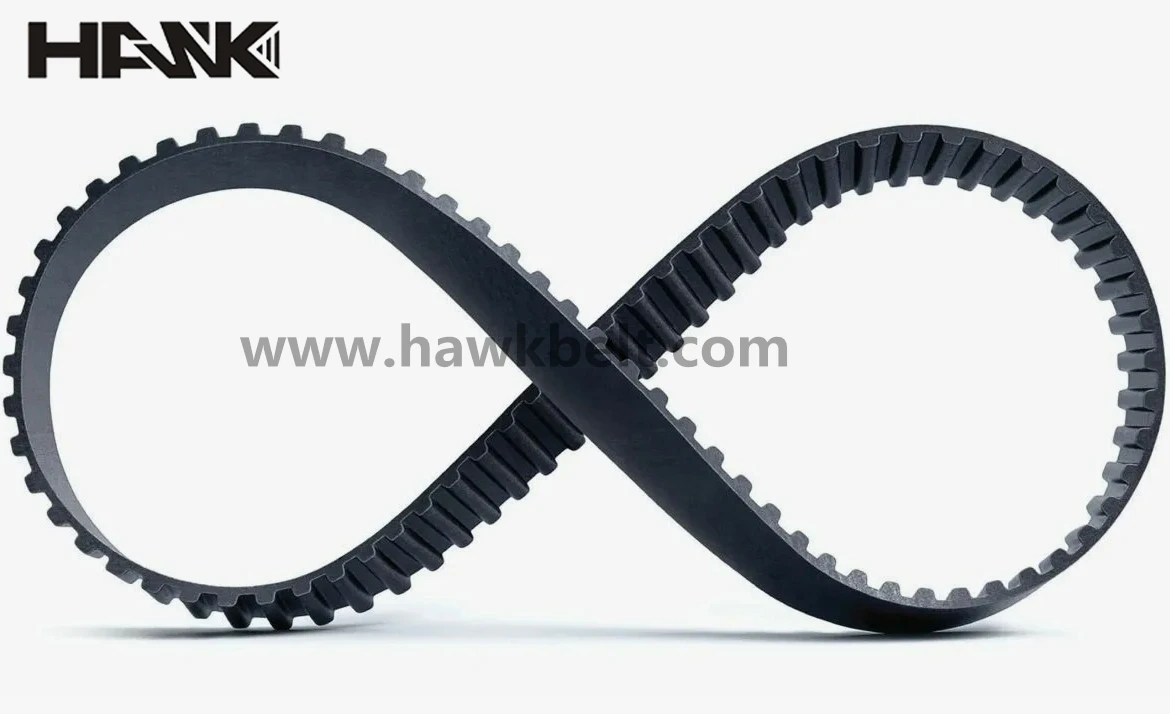
However, the theoretical specifications do not always translate perfectly into practice. Experienced technicians often encounter scenarios where a factory-recommended belt does not perform as expected due to modifications or wear and tear in the system. Here, genuine experience plays a pivotal role. Mechanics with years of hands-on experience can often determine the perfect belt by examining wear patterns on previous belts and assessing the condition of pulleys and tensioners.
fan belt size
When a standard size doesn’t fit, custom fan belts may become necessary. Reputable manufacturers offer bespoke solutions tailored to unique system configurations. Engaging directly with these manufacturers not only guarantees the acquisition of a belt optimized for your system but also provides access to their industry expertise. Many such companies have in-house engineers who can provide technical support, ensuring a seamless transition from an ill-fitting component to a perfectly adjusted one.
Quality control is another facet demanding attention.
Not all fan belts boast the same durability and performance capabilities. Brands with a longstanding reputation for quality and reliability, such as Gates or Continental, are more likely to offer products that withstand harsh operating conditions. Investing in these trusted brands may initially seem costly, but the superior performance and extended lifespan offer significant long-term savings.
Finally, regular maintenance is vital for retaining the optimal performance of any fan belt. This includes routine inspections for cracks, frays, or any sign of material degradation. Rotating parts like belts are subject to constant stress and, as such, require periodic adjustment and eventual replacement. Implementing a regular maintenance schedule, combined with utilizing high-quality belts, can greatly enhance operational efficiency and reliability.
In summary, ensuring that you have the correct fan belt size is not just about adhering to manufacturer guidelines but also incorporating the practical wisdom gained from real-world experience. Professionals who engage with this process regularly provide invaluable insights and enhancements tailored to unique operational contexts. Whether it’s through consulting technical support from a recognized manufacturer or engaging a seasoned mechanic, investing in the right resources is crucial, ensuring that machinery operates efficiently and sustainably for years to come.