Belts for pulleys are an essential component in a wide variety of machines and applications, playing a crucial role in the transfer of motion and force. These belts are not just a means of operation but an enabler of efficiency, performance, and productivity across diverse industries. Whether you’re a seasoned engineer or a newcomer looking to understand the nuts and bolts of pulley systems, this article provides valuable insights anchored in experience, expertise, authoritativeness, and trustworthiness.
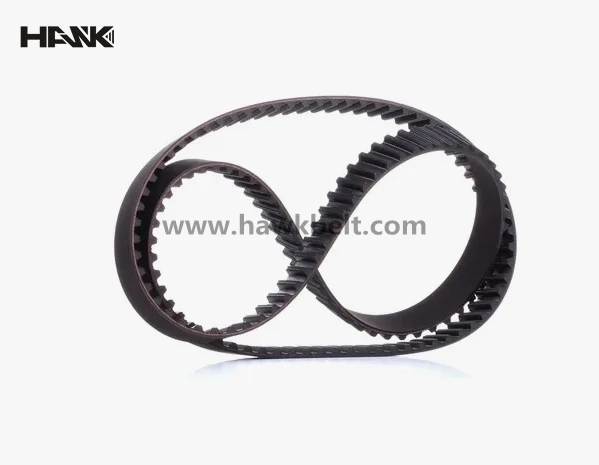
When selecting a belt for a pulley system, the compatibility between the belt and the pulley is paramount. Several types of belts are designed to accommodate different operational needs, including V-belts, timing belts, flat belts, and round belts. Each type is tailored to specific applications, offering distinct advantages and ideal for certain mechanical settings. For instance, V-belts are known for their high power transfer capabilities and are commonly used in automotive and industrial applications due to their durability and flexibility.
Understanding the materials used in belt manufacturing is essential for making informed purchasing decisions. Rubber, polyurethane, and neoprene are some popular materials that define the belt's ability to withstand wear and tear, resist chemical exposure, and perform under varying temperature conditions. Rubber belts are celebrated for their elasticity and grip, making them a preferred choice in conveyor systems. In contrast, polyurethane belts offer superior resistance to oils and can handle high loads, making them indispensable in heavy-duty machinery.
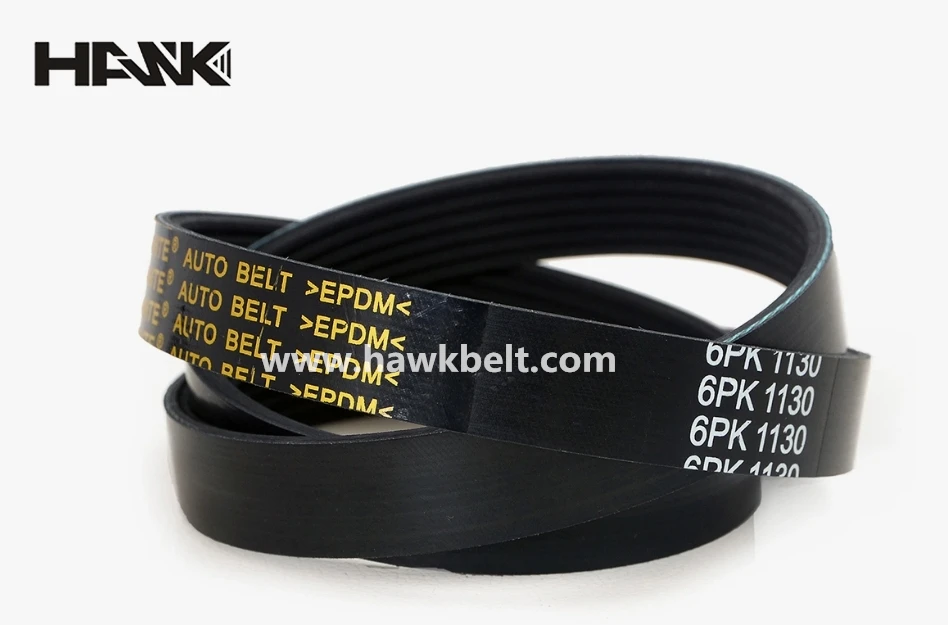
Expertise in the selection process extends to considering the operational environment of the pulley system. If the system operates in an environment subject to extreme temperatures, moisture, or chemical exposure, selecting a belt that can endure such conditions is crucial for longevity and performance. Consulting with manufacturers and technical specialists can provide clarity and reinforce decision-making with authoritative insights and tailored recommendations.
belt for pully
The intricacies of belt tensioning cannot be overlooked and are crucial for maximizing system efficiency. Proper tension ensures that the belt remains in contact with the pulley’s surface, reducing the chances of slippage and prolonging the life of both the belt and the pulley. Over-tensioning can lead to excessive wear and tear, while under-tensioning may result in inefficiencies and mechanical failures. Employing precision instruments, like tension meters, and adhering to manufacturer specifications, ensures optimal tension levels, further reflecting the importance of expertise and technical guidance.
For businesses and operators looking to build trust and confidence in their pulley systems, regular maintenance and inspection are essential practices. Humane Machine and OSHA guidelines suggest periodic examinations to prevent unexpected downtimes and safety hazards. Inspections should focus on identifying early signs of wear or misalignment, and proactive replacement of worn-out belts can forestall operational disruptions and costly repairs.
Furthermore, a keen understanding of regulatory compliance and safety standards ensures the trustworthiness of your operations. Adhering to guidelines stipulated by engineering standards such as the ISO, ASME, or local regulatory bodies establishes a framework of reliability and accountability.
In sum, when navigating the complex landscape of belts and pulleys, relying on experience and expertise is indispensable. Partnering with reputable suppliers known for quality and consistency enhances authoritativeness, ensuring that the belts are not only right for the application but also align with industry standards and best practices. Through diligent selection, precise tensioning, regular maintenance, and compliance with safety regulations, the life and efficacy of a belt and pulley system can be maximized, making it a cornerstone of dependable mechanical operations.