In the labyrinth of mechanical devices, motor belts stand as unsung heroes, propelling the motion required for operations across various industries. Much like the veins of a machine, these belts ensure smooth, consistent, and reliable performance wherever they are deployed. A comprehensive understanding of motor belts, from experience to expertise, is essential for businesses seeking efficiency and longevity in their machinery.
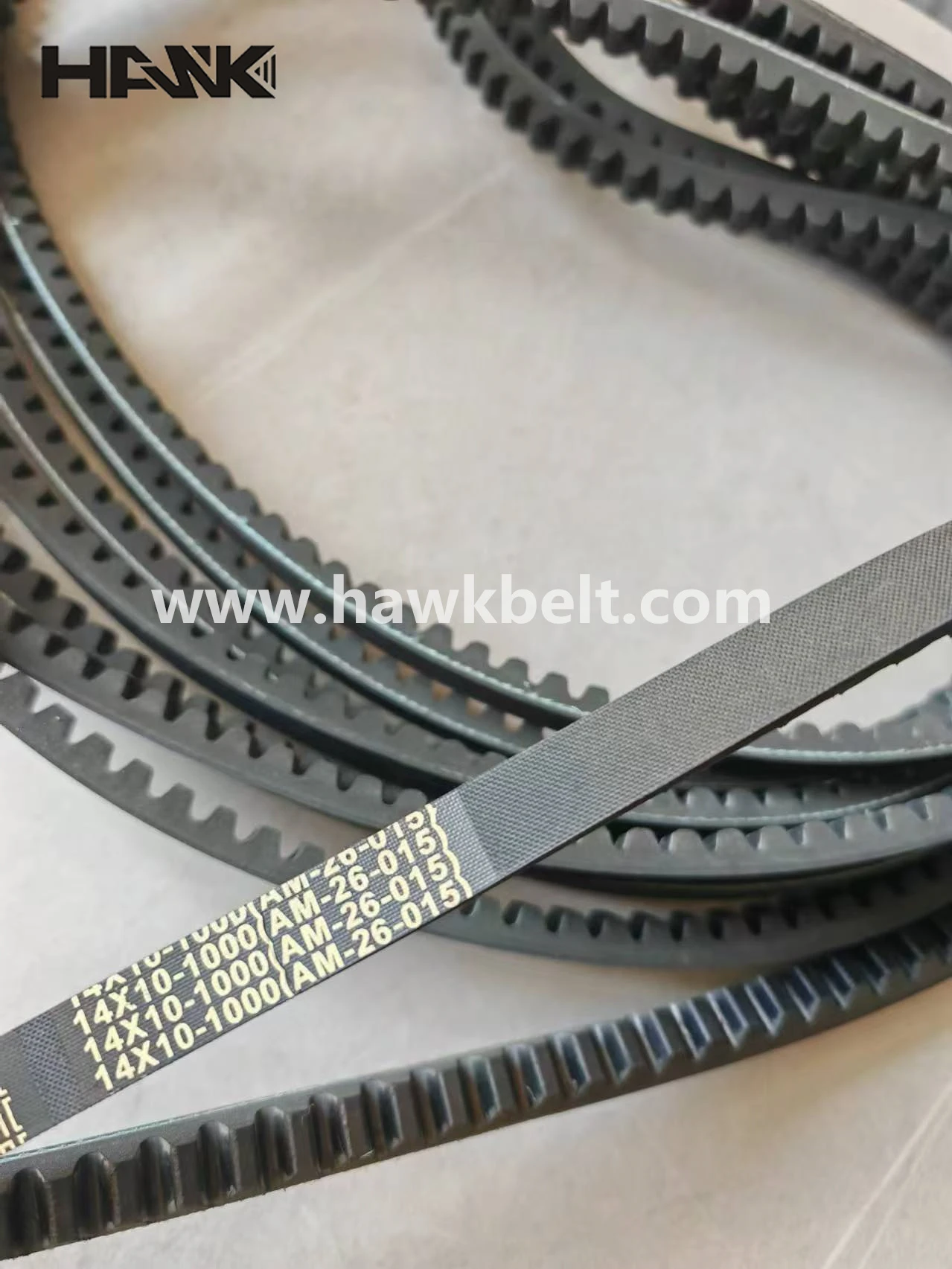
Motor belts, often referred to as drive belts, are flexible loops of durable material that mechanically link two or more rotating shafts, typically transferring energy from motors to other components. Whether in the automotive industry, HVAC systems, or manufacturing equipment, the role of motor belts is critical, demanding a suitable choice based on specific applications and conditions.
Experience dictates that selecting the right type of motor belt can significantly impact machine performance. Professionals recommend starting with an analysis of the operational environment—considering factors such as temperature, exposure to chemicals, and the belt's mechanical load. For instance, in applications exposed to high heat, V-belts made of materials like neoprene or ethylene propylene diene monomer (EPDM) offer resilience and longevity. Meanwhile, for environments where chemical exposure is a concern, polyurethane or rubber belts might be preferable to prevent degradation and ensure service reliability.
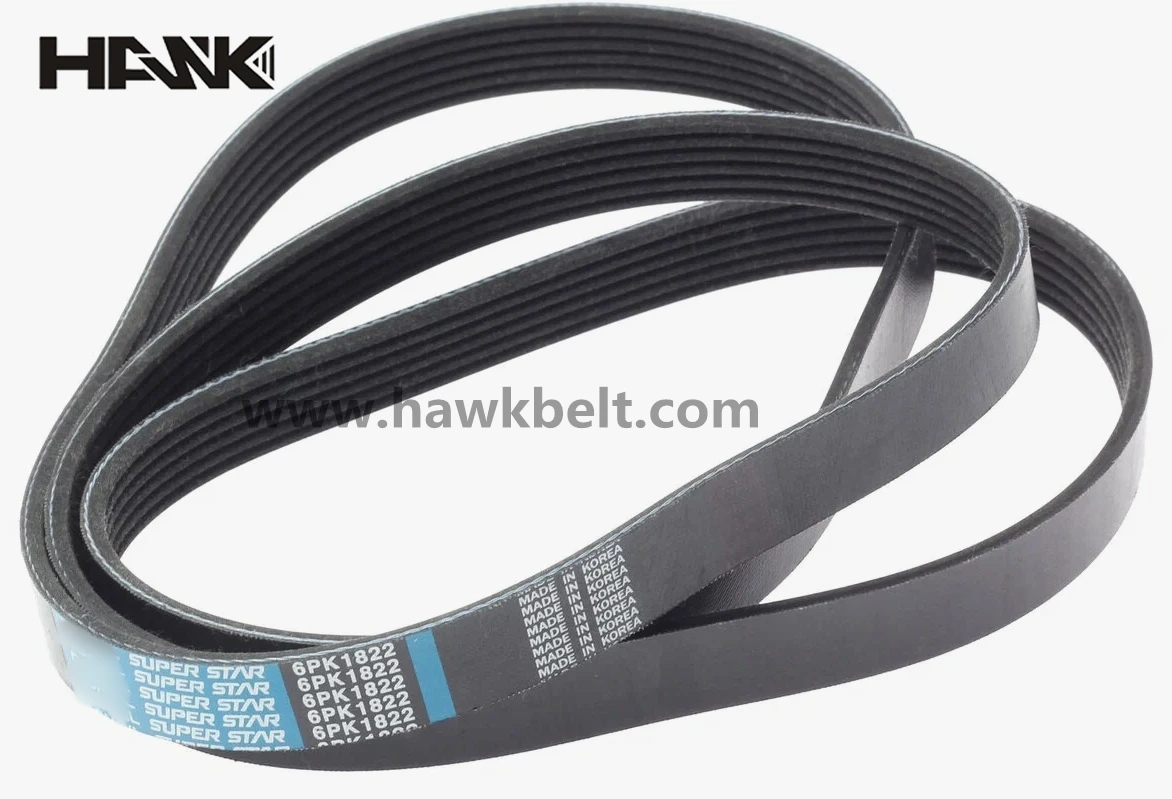
Expertise in the field of motor belts emphasizes the significance of tension adjustment. Proper tension is a balancing act; too tight a belt might put undue stress on bearings and motors, shortening their lifespan, while a too-loose belt can lead to slippage and energy loss. Utilizing tools like a tension gauge can help in measuring and adjusting the tension accurately, contributing significantly to the overall efficiency and durability of the machinery.
motor belts
Authoritativeness is further established by drawing on industry-specific standards and recommendations. For example, the International Organization for Standardization (ISO) and the Association for Advancing Automation (A3) provide guidelines and best practices for maintaining belt drives. Adhering to these standards not only helps in optimizing performance but also in ensuring compliance, which can be crucial for industry certifications and audits.
Trustworthiness, in the context of motor belts, often comes down to the choice of brands and the quality of components. Brands like Gates, Dayco, and Continental have built reputations over decades, offering products that are known for their quality and reliability. Investing in reputable brands might come with a higher initial cost, but it pays dividends in reduced maintenance needs and fewer replacements over time. Furthermore, it is advisable to source belts from authorized distributors to avoid counterfeit products that can jeopardize operations and safety.
An often-overlooked aspect is the role of regular maintenance and monitoring.
Industry veterans would argue that even the best motor belt cannot offset the consequences of negligence. Scheduled inspections, focusing on signs of wear, tear, or misalignment, should be part of routine maintenance. Utilizing smart sensors and IoT devices can automate this process, providing real-time data on the belt's condition and allowing for predictive maintenance strategies.
In conclusion, motor belts play a pivotal role in the world of mechanization, bridging the gap between energy output and functional application. An understanding grounded in real-world experience and industry expertise can guide the selection and maintenance of these components, ensuring optimal performance and reliability. By aligning with authoritative practices and investing in trustworthy products, businesses not only safeguard their operations but also drive their growth and innovation.