Heat joining in drive belts is a transformative process that merges engineering prowess with nuanced understanding to produce belts capable of withstanding rigorous industrial demands. An in-depth exploration into the anatomy, benefits, and implementation techniques of heat joining provides vital insights into why this method is lauded as an industry benchmark.
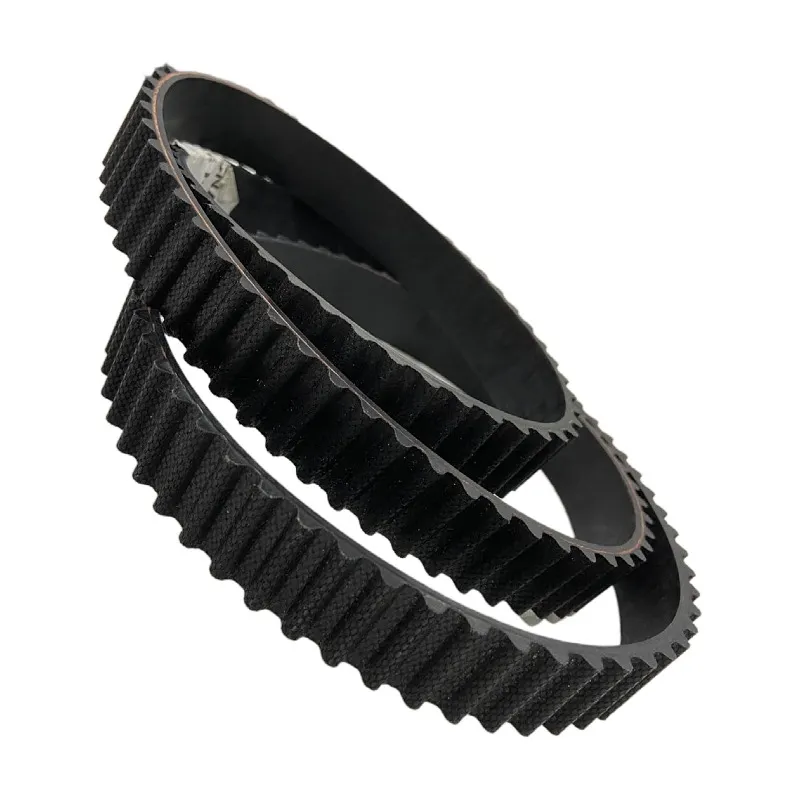
Drive belts, integral to powering machinery, operate under variable conditions and constraints. Their reliability is non-negotiable, necessitating precision in construction—this is where heat joining shines. This advanced technique involves fusing belt ends using controlled thermal exposure, ensuring seamless integration and enhanced durability. Craftsmen in this space appreciate the methodology for its capacity to balance flexibility with robustness, offering unparalleled continuity that mechanical joining methods often lack.
The process begins with carefully preparing the belt ends. Each end is meticulously cut and aligned to eliminate any deviation that could compromise the join integrity. The heat application follows—a calibrated procedure where temperature and duration are critical. Expertise is paramount here; excessive heat can degrade material fibers, while insufficient heat fails to achieve the necessary fusion. Tools for this process range from localized infrared heaters to precision heat presses, varying by manufacturer preference and belt composition.
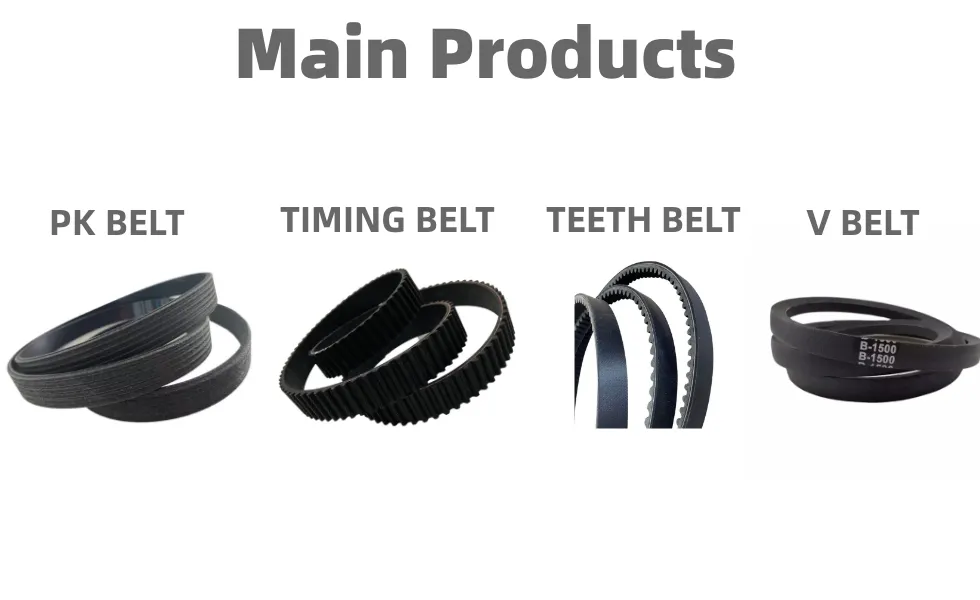
A core advantage of heat joining is the resultant belt's elongation resistance. Unlike mechanical fasteners, which can introduce points of weakness or uneven stress distributions, a heat-joined belt maintains uniform tension. This uniformity translates to longer operational life, reduced maintenance requirements, and ultimately, cost savings. For industries where downtime equates significant financial loss, such resilience is invaluable.
Moreover, the methodology prevents the ingress of debris and particles that are potential contaminants in mechanically fastened belts. In high-purity environments like pharmaceuticals and food processing, maintaining an unbroken belt surface is critical. Heat joining inherently supports these cleanroom stipulations by ensuring that the belt’s surface remains smooth and impermeable.
heat joining drive belt
Trust in this technology is cemented by exhaustive testing and industry validation. Various dynamic and static tests under simulated operational conditions reaffirm that heat-joined belts exhibit superior lifespan and reliability. Experts continually refine techniques, adopting new materials and heat sources, aligning with sustainable and resource-efficient practices.
Nevertheless, successful heat joining is contingent upon the expertise of the technician. Mastery over the thermal properties of diverse materials – from rubber-based composites to high-strength polymers – dictates the outcome. Training programs and technical certifications often reinforce this expertise, pushing industry standards upwards.
As industries evolve, so do belt applications, from traditional conveyor systems to precision robotics. Each application demands specific performance characteristics that heat joining readily adapts to. OEMs and maintenance professionals consistently choose heat joining for its adaptability and proven track record.
Recent advancements in automated heat joining systems promise even more consistent results. Automation minimizes human error, offering precision tuning and repeatability that sets new benchmarks. As these technologies intersect, the field moves towards a future where precision-engineered belts support ever more complex industrial frameworks.
In conclusion,
heat joining revolutionizes the conventional wisdom of belt fabrication. It embodies a synthesis of technical expertise, material science, and practical application, enhancing belt performance across diverse sectors. As industries demand more from their machinery, the significance of robust, seamlessly joined belts cannot be overstated—a testament to heat joining's pivotal role in modern industrial output.