In the realm of power transmission and mechanical engineering, toothed belts, often referred to as timing belts or synchronous belts, have carved a niche of their own. Known for their precise motion control, these belts have become indispensable in various industries, offering unique advantages that cater to the multifaceted needs of modern machinery.
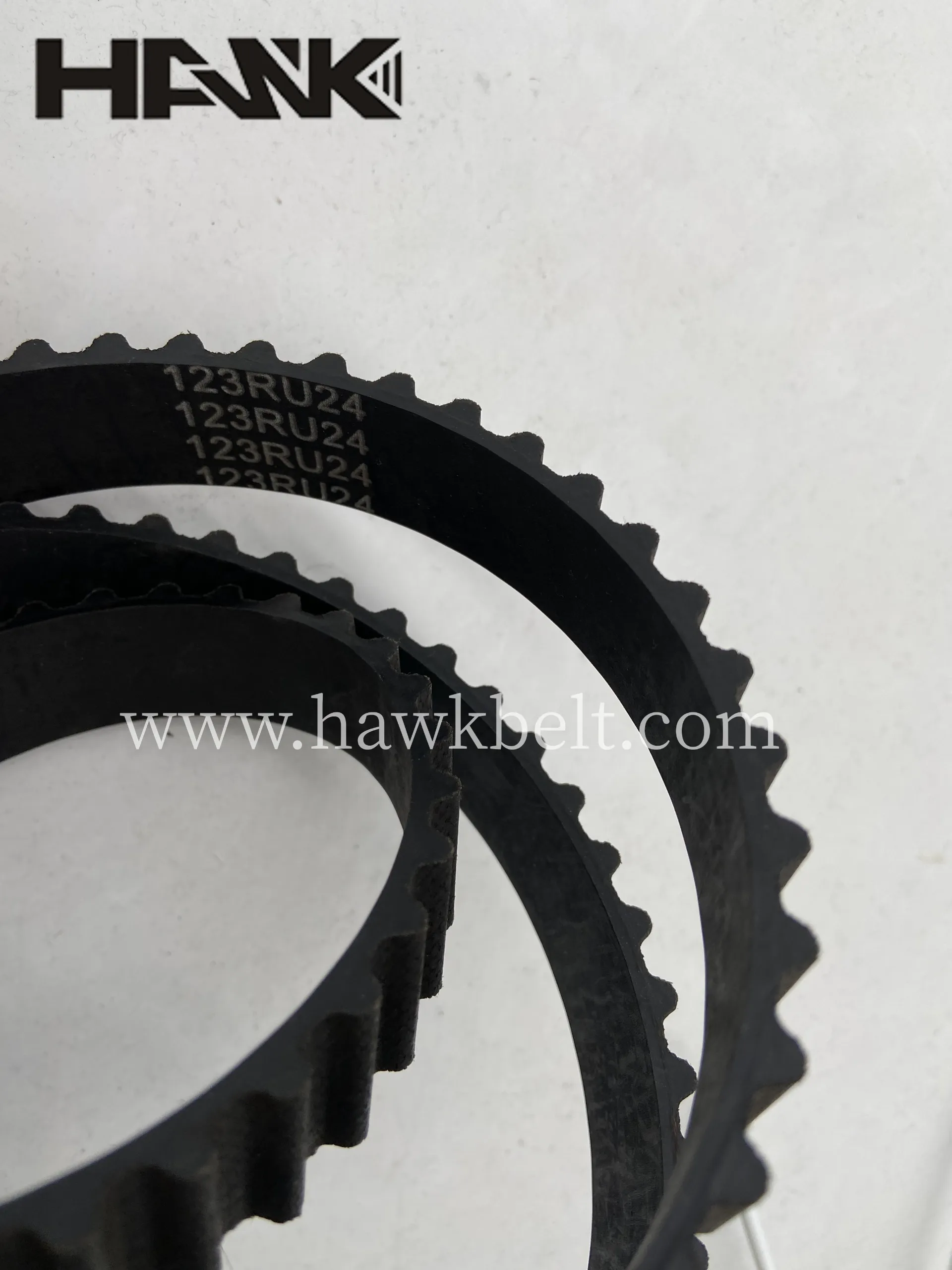
A toothed belt is engineered to mesh perfectly with the grooves of compatible pulleys, ensuring synchronous transmission of power. This ingenious design prevents slippage and maintains a constant angular velocity ratio, which is critical in applications such as automotive engine timing, conveying systems, and robotics. These capabilities underscore the belt's innate ability to provide efficiency and precision, making it a favored choice among engineers and DIY enthusiasts alike.
One of the defining features of toothed belts is their capacity to deliver noise-free operation. Unlike chains or gear drives, these belts eliminate metal-on-metal contact, resulting in significantly reduced operational noise. This makes them ideal for applications where a quiet environment is paramount, such as office equipment, textiles, and medical devices. Furthermore, the absence of lubrication requirements saves both cost and maintenance time, further enhancing their appeal.
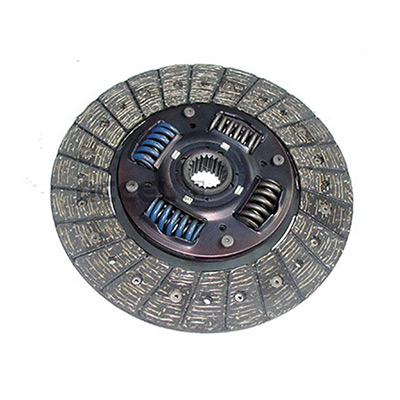
Durability is yet another forte of toothed belts. Constructed with high-strength materials like neoprene or polyurethane, often reinforced with fiber cords such as fiberglass or Kevlar, these belts exhibit remarkable resistance to wear and environmental degradation. This robustness ensures a prolonged service life, even under harsh operating conditions, thereby reassuring users of their reliability and cost-effectiveness over time.
Innovative advancements in material science continue to bolster the versatility of toothed belts. New composite materials and reinforced constructions are continuously being developed to enhance performance, thermal resistance, and chemical stability. This evolution allows the belts to meet the demanding needs of emerging technologies and industries, ensuring they remain at the forefront of mechanical design.
toothed belt
In terms of customization, toothed belts offer a plethora of options, catering to various specifications and constraints. From standard trapezoidal tooth profiles to more intricate curvilinear designs, engineers can select or design a belt that perfectly aligns with the specific requirements of their machinery.
This adaptability is instrumental in optimizing machine performance and boosting overall productivity.
Safety and reliability are non-negotiable aspects in the design of modern machinery, and toothed belts excel in delivering both. Their non-slip characteristic ensures accurate, repeatable movements, crucial in applications like automated production lines and precision instruments. By minimizing the risk of operational errors or misalignments, these belts contribute to safer, more reliable systems.
The environmental impact of mechanical components is increasingly scrutinized in our eco-conscious world. Toothed belts, with their long lifespan and minimal maintenance needs, surface as an environmentally friendly choice. Their efficiency in power transmission contributes to reduced energy consumption, aligning with the global shift towards green manufacturing practices.
In conclusion, toothed belts offer a synthesis of precision, efficiency, and reliability that few other mechanical components can match. Their application spans across diverse industries, from automotive to electronics, each benefiting from the belt's unique properties. As technology advances and new demands manifest, the evolution of toothed belts promises continued relevance and innovation, cementing their place as a cornerstone in the world of power transmission. For those seeking a mechanism that embodies excellence in performance and efficiency, the toothed belt remains an ever-reliable choice.