Toothed drive belts, often referred to as timing belts or synchronous belts, play a crucial role in a variety of mechanical applications, from automotive engines to precision machinery. These components are integral to the seamless operation of complex systems, ensuring synchronized movement between different parts without slippage. The unique design of toothed drive belts, featuring teeth that mesh with the corresponding grooves in the pulleys, provides exceptional efficiency and reliability.
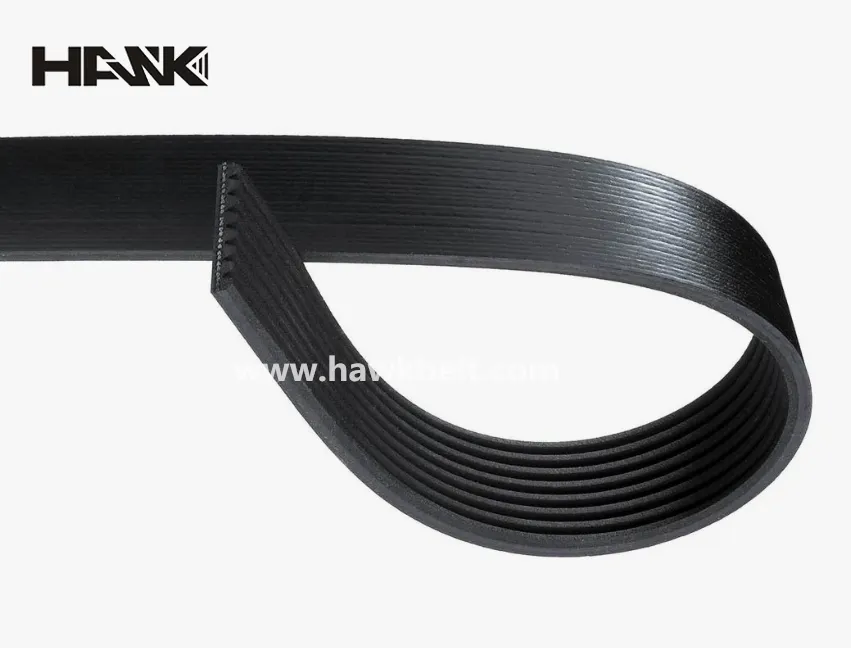
One of the primary advantages of toothed drive belts over traditional V-belts or flat belts is their ability to maintain a fixed speed ratio between connected components. This eliminates the chance of slippage, which can cause timing errors and lead to mechanical failures. This characteristic makes toothed drive belts particularly valuable in applications where precision is paramount, such as in automotive engines where they regulate the timing of camshafts and crankshafts to ensure optimal engine performance.
From an expert's perspective, the selection of a toothed drive belt involves several critical considerations. Material choice is at the forefront. Modern toothed drive belts are typically made from high-strength rubber compounds reinforced with fibrous materials like fiberglass, nylon, or even Kevlar. This construction provides an ideal balance between flexibility, durability, and resistance to environmental factors such as temperature fluctuations and exposure to oil or chemicals.
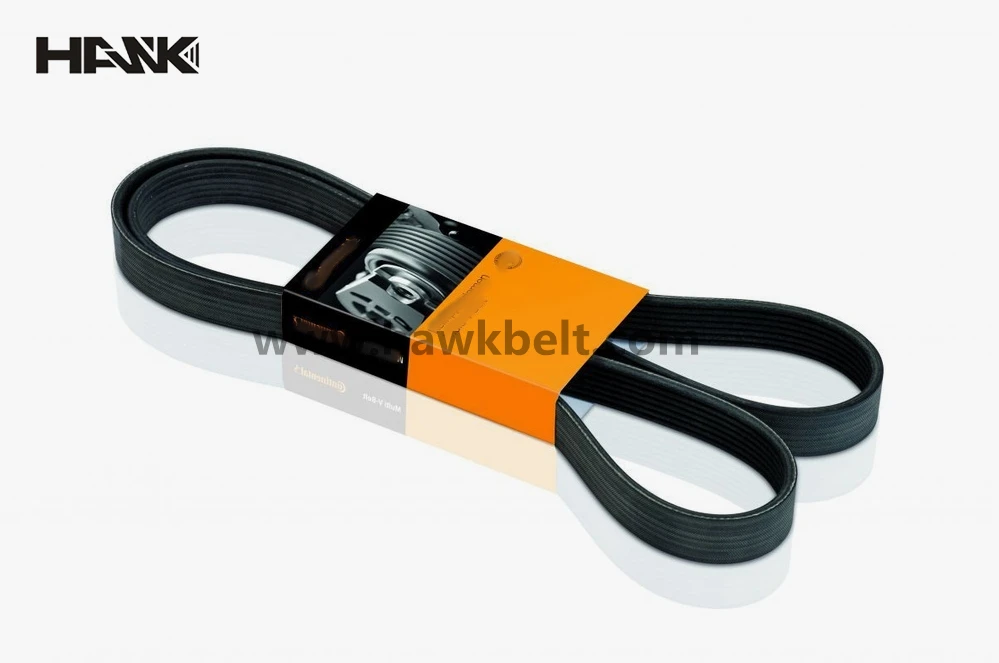
Durability is a key indicator of a toothed drive belt's performance. Regular maintenance checks and timely replacements are essential to avoid unexpected downtimes. Users with hands-on experience often recommend inspecting belts for signs of wear or damage, such as fraying, cracking, or glazing. Keeping an eye on the tension is equally important, as improper tension can lead to premature wear or, in worst-case scenarios, belt failure.
toothed drive belts
The technological advancements and innovations in the field of toothed drive belts have led to the development of specialized belt types tailored for specific applications. High torque drive belts, for example, are designed to handle heavier loads, while miniature belts are crafted for compact devices that require precise motion control. By choosing the right type of belt for the specific application, users can greatly enhance system efficiency and longevity.
Understanding the authoritative recommendations from leading manufacturers can significantly impact the decision-making process. Brands with a long-standing reputation in the industry often provide comprehensive support through detailed product guides and technical specifications. These resources guide users in matching belt parameters such as pitch, length, and width to their specific needs, thus fostering trust in their product offerings.
Emphasizing reliability, toothed drive belts reduce the need for frequent adjustments and maintenance, granting systems higher availability rates. Trust in toothed drive belts comes from their proven track record of performance in rigorous settings, supported by endorsements and testimonials from professionals who rely on them daily in high-stakes environments.
In conclusion, toothed drive belts are indispensable mechanical components that provide precision, reliability, and efficiency across numerous industries. Their careful selection and maintenance, guided by expert insights and manufacturer recommendations, ensure seamless operation and longevity. By leveraging the latest advancements in materials and design, users can unlock the full potential of their mechanical systems, confident in the power of toothed drive belts to synchronize and optimize operations.