Flat rubber belts serve as a critical component in a multitude of industrial applications, offering efficiency, durability, and performance in power transmission. Understanding these belts' materials is paramount for industries ranging from manufacturing to automotive. This article delves into the specialized properties and advantages of flat rubber belt materials, ensuring businesses can make informed decisions for their mechanized operations.
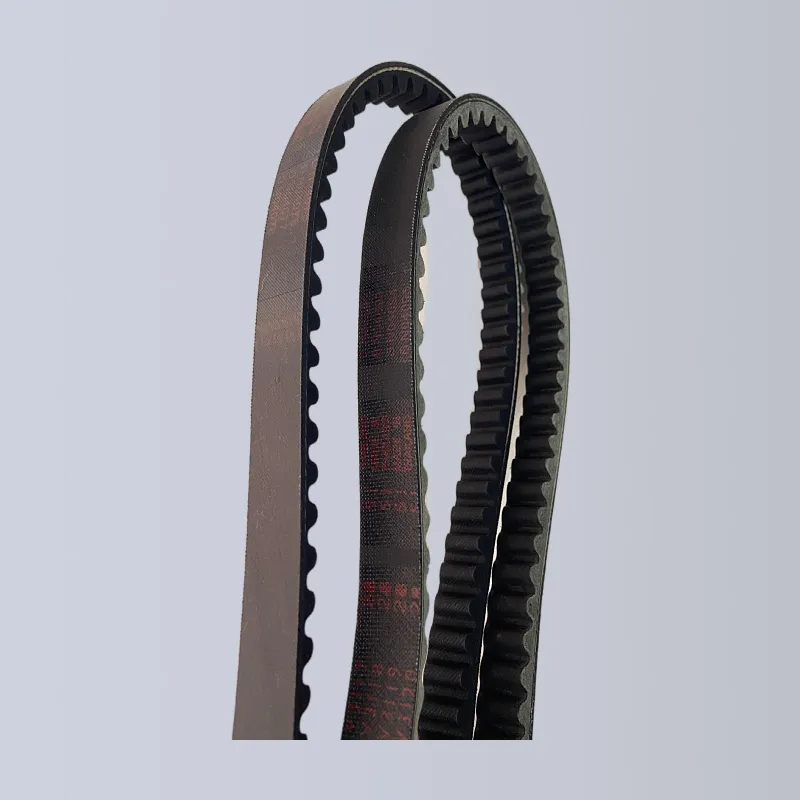
Rubber, as a versatile material, exhibits natural elasticity and durability, making it ideal for belt manufacturing. The flat configuration provides uniform pressure distribution across surfaces, reducing slippage and wear while maximizing efficiency. One of the standout materials used in these belts is neoprene, known for its exceptional resistance to oils, chemicals, and temperature extremes, making it particularly suitable for demanding environments where longevity and resilience are essential.
Moreover, natural rubber remains a popular choice for flat belt production due to its flexibility and shock-absorbing capabilities. Its inherent tackiness aids in gripping pulleys, which is crucial for applications requiring precise power transmission. Despite its susceptibility to environmental wear, advancements in compounding have significantly extended its lifespan and performance capabilities.
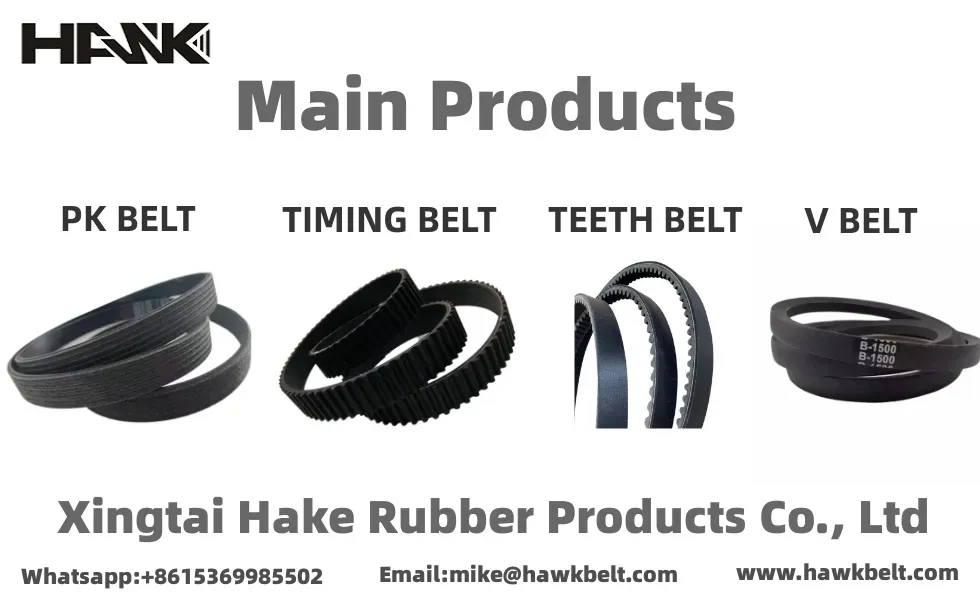
Next is nitrile rubber (NBR), which excels in environments exposed to oils and grease. NBR flat belts provide superior resistance to these elements, making them indispensable in automotive and machinery sectors where lubricants are prevalent. Their cost-effectiveness and performance ratio make them a go-to choice for many engineers and OEMs.
EPDM (ethylene propylene diene monomer) is another noteworthy material in the flat rubber belt space. Known for its resistance to weathering, ozone, and heat, EPDM is used extensively in outdoor applications and those involving high temperatures. Its application is evident in agriculture and landscaping machinery that operate in various climates and weather conditions.
The industrial revolution has ushered in synthetic rubber variations, such as polyurethane and silicone, each offering unique benefits. Polyurethane flat belts boast high load capacity and abrasion resistance. They are particularly suited for conveyor systems within manufacturing plants, where they withstand continuous operation and transport heavy loads with minimal maintenance requirements.
flat rubber belt material
Alternatively, silicone rubber belts offer unparalleled thermal stability and resistance to extreme temperatures, both high and low. These properties are leveraged in industries such as food processing and packaging, where sterilization and exposure to fluctuating temperatures are routine.
For any business considering flat rubber belts, understanding the interplay of material properties and operational conditions is crucial. Selection not only impacts the immediate efficiency but also the long-term viability and cost-effectiveness of machinery. The right material choice can enhance energy savings, reduce downtime, and prolong the service life of both the belt and the machinery it powers.
Besides material selection, attention to the belt's surface finish and construction can significantly affect performance. Precision in manufacturing processes ensures consistent thickness and elasticity, which are vital for achieving balanced power transmission and reducing the chances of operational failure.
Moreover, considering environmental impact has become an essential part of material selection. Many manufacturers are now prioritizing sustainable materials and eco-friendly processes to align with global efforts in reducing carbon footprints. Recyclable rubber compounds and reduced energy consumption in manufacturing processes are increasingly integrated into belt production, supporting green engineering initiatives.
Finally, consultation with experienced suppliers and engineers can lead to better material selection tailored to specific applications. These professionals bring expertise and industry insights, offering authoritative guidance that combines both technical specifications and practical implications.
The evolution of flat rubber belt materials continues to advance, driven by technological progress and environmental considerations. Businesses investing in understanding these materials harness not only enhanced operational efficiencies but also contribute to broader sustainability goals in modern industrial practices.