Mastering the process of installing a new serpentine belt is a critical skill for car enthusiasts and do-it-yourself mechanics. Of all vehicle maintenance tasks, this one combines mechanical skill with strategic planning. While it may seem straightforward at first glance, replacing a serpentine belt involves both art and engineering, ensuring the belt achieves perfect tension and alignment for optimal vehicle performance.
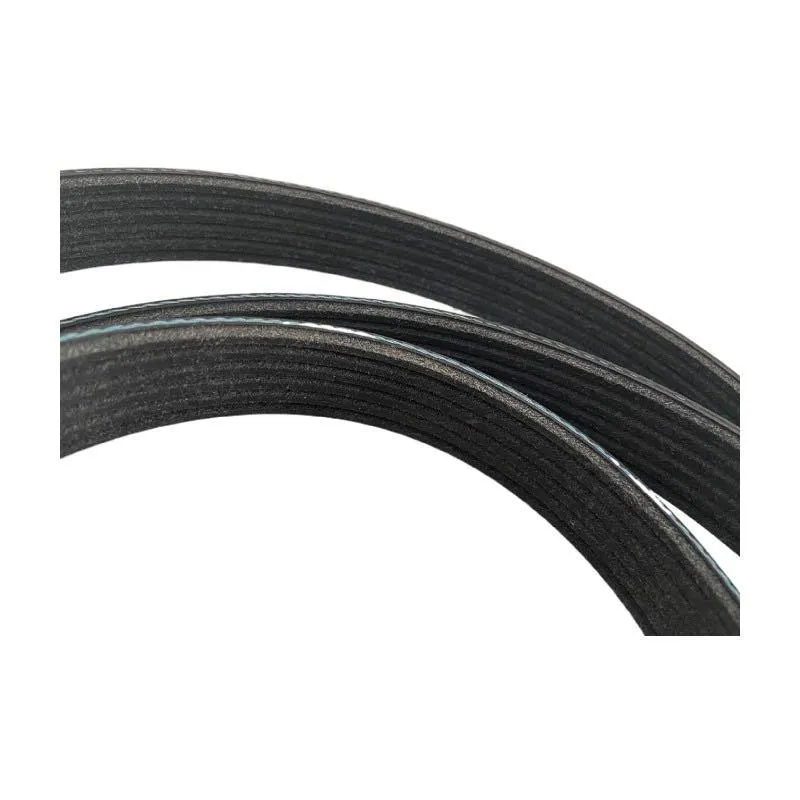
To begin, a serpentine belt is a single, continuous belt used to drive multiple peripheral devices in a car’s engine, such as the alternator, power steering pump, water pump, air conditioning compressor, and sometimes the cooling fan. Once you understand its essential role, the necessity of replacing it becomes clear when signs of wear appear.
1. Recognizing Wear and Tear
Every vehicle owner should regularly inspect the serpentine belt as part of routine maintenance. Look for frays, cracks, or signs of excessive wear. A squealing noise coming from the engine bay often signals a failing belt, indicating that replacement is overdue. Neglecting these indicators could lead to serious mechanical failures and costly repairs.
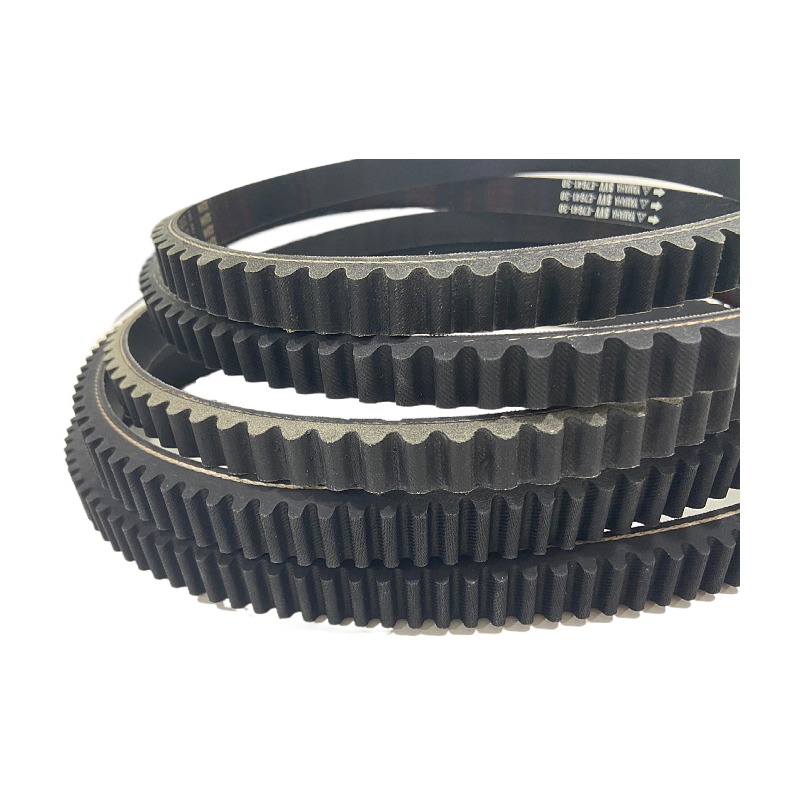
2. Gathering the Necessary Tools
Successful installation begins with preparation. Essential tools usually include a ratchet with socket set, belt tensioner tool, and a serpentine belt diagram for your specific vehicle make and model. Always consult your vehicle’s manual for the specific requirements and diagrams, ensuring the right belt is purchased.
3. Safety First
Prior to any mechanical work, ensure that the vehicle is parked on a flat surface, the engine is cool, and the keys are removed from the ignition. Disconnect the battery to prevent accidental startups or electrical shorts during the belt replacement.
4. Removing the Old Belt
Begin by locating the belt tensioner. This component is pivotal for adjusting and removing the belt. Use a wrench or belt tensioner tool to pivot the tensioner, releasing the belt's tension, and carefully slide the belt off the pulleys. It's crucial to note the routing path before removing the old belt. Many vehicles have a decal under the hood with this information.
installing new serpentine belt
5. Inspecting the Pulley System
With the old belt removed, now is the opportune time to inspect the pulleys. Spin each by hand; they should rotate freely without obstruction or noise. Any roughness or vibrations could indicate a bearing issue, warranting immediate attention before proceeding with the new belt installation.
6. Installing the New Belt
Follow the belt routing diagram to weave the new serpentine belt through the pulleys. It should fit snugly along each pulley groove without excessive slack. Once routed, apply tension by reengaging the belt tensioner. Double-check the alignment to prevent future slippage or wear.
7. Final Inspection
Before starting the engine, perform a thorough inspection. Ensure that the belt is seated correctly on each pulley and retains the appropriate tension. Reconnect the battery and start the engine, observing for any unusual sounds or belt movement, which could indicate improper installation.
8. Post-Installation Maintenance
After installation, the new belt will require a break-in period. Recheck the belt and tension after approximately 100 miles to ensure everything remains secure and correctly aligned. Regular bi-annual inspections can prolong the life of the belt and save significant repair costs over the vehicle's lifespan.
Proficiency in installing a new serpentine belt aligns with a broader commitment to vehicle maintenance. By following the outlined steps and maintaining vigilance with regular checks, one can ensure that their vehicle runs smoothly, minimizing the risk of unexpected breakdowns. This task not only enhances your mechanical expertise but also imbues a sense of authority and trust, knowing that your vehicle’s performance is maintained through careful, expert attention.